Blogs
What is OEE and Why It’s Crucial for Manufacturing Success
Introduction
In a manufacturing environment, productivity and efficiency are critical. The most popular metric to measure this efficiency is OEE (Overall Equipment Effectiveness), which indicates valuable insights. In this blog, we'll see what OEE is, how it is calculated, and why it plays a crucial role in manufacturing success.
Whether you are planning to minimize waste and downtime or consistency of the product, this will help you to understand and apply OEE to stay with you more competitively compared to others.
Wondering How OEE Can Boost Efficiency?
Connect with our experts today to see how OEE can transform your production.
Table of Contents
Understanding Overall Equipment Effectiveness (OEE)
What is OEE?
OEE is the Norm for measuring the efficiency of the manufacturing process. It connects three primary Metrics availability, performance, and quality, into an Overall Rating that reflects how efficiently equipment is used.
Three Core Metrics of OEE: Availability, Performance, and Quality
Availability: Calculates the percentage of planned time that equipment is actually working.
Performance: Examines maximum speed of the machinery if that is operating.
Quality: Analyzes the ratio of the product that meets our quality Requirement.
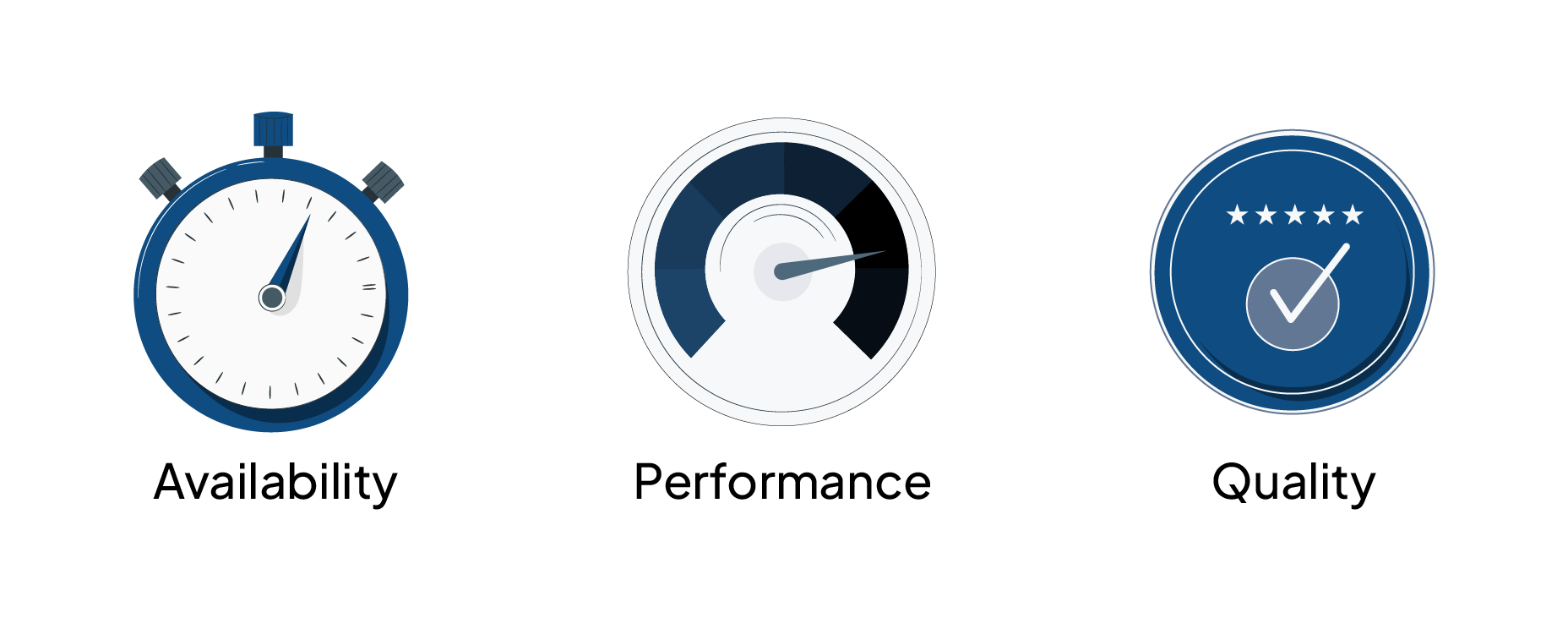
Find Hidden Efficiency Gains!
Book a free consultation to uncover key improvement areas with OEE
How to Calculate OEE
Calculating OEE involves three significant key factors: Availability, Performance, and quality. All of these factors deliver valuable insights into various aspects of machine or equipment effectiveness, which can be combined to provide a Calculated OEE score.
Step-by-Step CalculationTo calculate your OEE precisely, you need to fetch the correct data from your production line. Let's break down the calculation's three major components and describe how to sort out the value.
To calculate OEE, follow these steps:
- Availability = Operating Time / Planned Production Time
- Performance = (Ideal Cycle Time × Total Pieces) / Operating Time
- Quality = Good Pieces / Total Pieces
Availability
Availability measures how long your equipment is actively running compared to the scheduled production time. This component will identify any unscheduled downtime, such as breakdowns and stoppages. Effectively, it answers the question, "How much of the scheduled time was the equipment actually available to produce?"
Formula :
Total available time for production, except planned breaks, maintenance, or shift charges.
Operating Time :To indicate the actual time the equipment runs and produces goods. This except the breakdowns, maintenance, or any other interruptions due to downtime
For example, if the planned production time for a shift is 8 hours (480 minutes), but the equipment was only running for 7 hours (420 minutes) due to downtime, the Availability would be:

Performance
Performance indicates how effectively equipment operates when it is running. It compares the actual production rate to the ideal production rate.

The total number of units produced during the operating time.
Operating Time :The actual time the machine was in operation.
For instance, if the ideal cycle time is 2 minutes per piece, and 200 pieces were produced during 420 minutes of operating time, the Performance would be calculated as:

Quality
Quality evaluates the ratio of products that match required quality standards out of the total number produced.
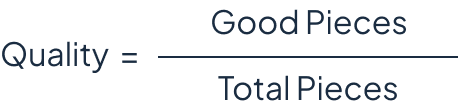
The number of units that pass quality inspections and meet the required standards.
Total Pieces :The total number of units produced during the operating time.
For example, if out of 200 pieces produced, 180 pass quality checks, the Quality score would be:

Let's imagine the machine is 87.5% available, 95.2% performance, and 90% quality. The OEE would be calculated by multiplying the above percentages. OEE=0.875×0.952×0.90=0.749 or 74.9% Therefore, the equipment is operating at 74.9% of its total potential efficiency. These OEE scores give insights into where improvements can be made, such as reducing downtime, improving speed, or increasing the quality of the products being produced.
The Importance of OEE in Manufacturing
In various manufacturing areas, OEE drives significant improvements by providing valuable insights into equipment performance. OEE helps identify inefficiencies and work toward smoother and more productive operations.
Improving Operational Efficiency
OEE serves as a source of guidance for finding areas of improvement and maximizing operational efficiency by analyzing performance data using Availability, performance, and quality metrics. Manufacturers can gain clear visibility into particular issues affecting their production lines. This will enable informed decisions about simplifying processes and resource allocation and achieving targeted improvement.
Minimizing Downtime and Waste
The two most significant factors in manufacturing operations are downtime and waste, which can affect profitability. With the help of OEE, manufacturers can easily detect and address sources of downtime and waste in real-time. OEE data report points out Occurrences when the machines are blocked, idle, or running below optimal speed; prevent these issues by allowing teams to take corrective actions without any escalating process
Enhancing Product Quality and Consistency
Building and Maintaining Trust with clients based on product quality and consistency directly impacts manufacturers' reputations and long-term success. A high OEE report indicates production is not only fast and efficient but also yields products that meet or exceed quality standards. The OEE quality component provides a precise measure of the number of products that meet the expected standards versus the number that require work or are considered waste.
Start Your Journey to Smarter Manufacturing
Get personalized recommendations for optimized production—contact us today!
Request a Free Consultation NowConclusion
Overall Equipment Effectiveness (OEE) is far more than just a performance metric. It's a significant tool that provides a roadmap for Reaching manufacturing excellence. By providing a detailed view of manufacturers' operations, OEE helps pinpoint inefficiencies, track progress, and implement strategies for continuous improvement, whether it's minimizing downtime, improving machine performance, or enhancing product quality. OEE delivers actionable insights that drive better decision-making at all levels of production. By adopting OEE and using it to inform their decision-making, manufacturers can position themselves for long-term success in a dynamic and increasingly digital manufacturing landscape.
Need support? Contact our team
Mon - Sat: 9 am to 6.30 pm
Leave a comment
Your email address will not be published. Required fields are marked *