Start Your Live Demo Now!
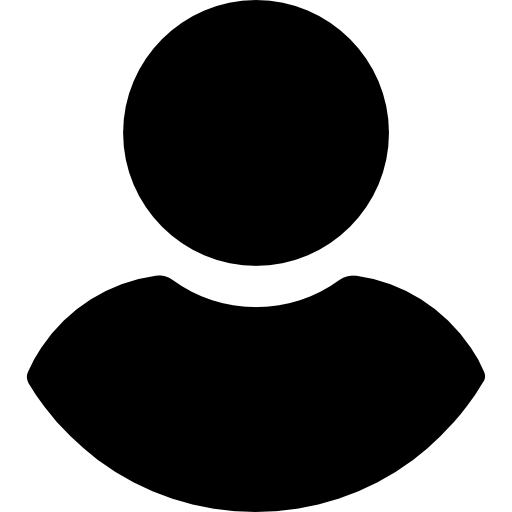
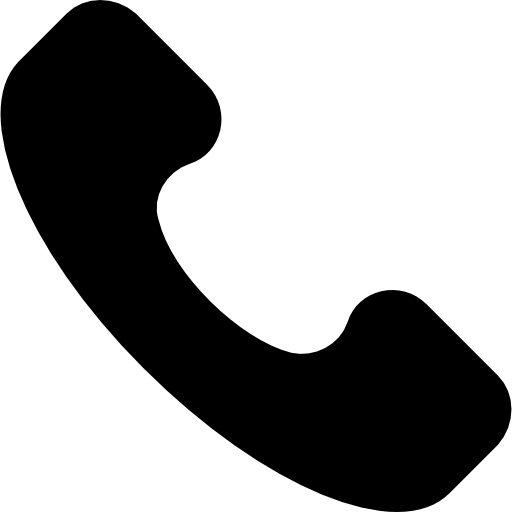
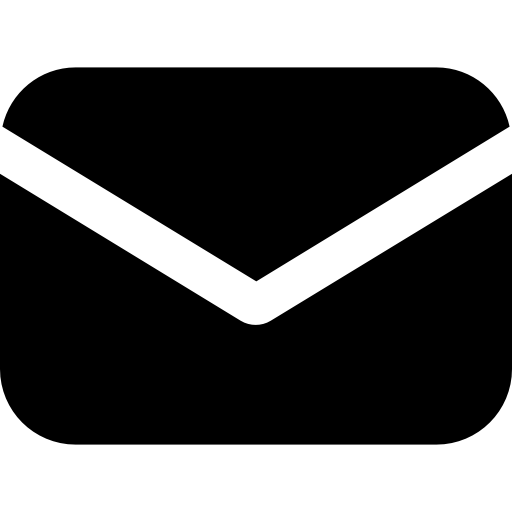
How Real-Time Production Monitoring Software Transforms Manufacturing Operations
Introduction
Manufacturing is evolving rapidly, and staying competitive requires more than just efficiency. It demands real-time insights, data-driven decisions, and optimized production processes. Traditional monitoring methods, such as manual data collection and reactive maintenance, often lead to inefficiencies, downtime, and increased costs. To address these challenges, modern manufacturers are turning to real-time production monitoring solutions like M-Connect. This advanced system provides real-time tracking of machine performance, employee productivity, and product quality, ensuring streamlined operations and continuous improvement. This blog explores the importance of production monitoring, the challenges of traditional methods, and how M-Connect is revolutionizing manufacturing efficiency.
Enhance Efficiency with Real-Time Monitoring
Schedule a Demo NowTable of Contents
The Importance of Production Monitoring in Manufacturing
Production monitoring is not just a buzzword. It’s a critical component of modern manufacturing that directly impacts a company’s ability to compete, grow, and thrive. In an industry where efficiency, quality, and timeliness are paramount, production monitoring provides the foundation for achieving these goals. Here’s a deeper look at why production monitoring is essential in manufacturing:
1. Real-Time Visibility into Operations
At its core, Work order management is the process of managing and tracking the lifecycle of work orders, from creation to completion. It ensures that maintenance tasks are efficiently executed, resources are optimally utilized, and any issues are promptly addressed.
For example, if a machine suddenly slows down or stops working, production monitoring systems can immediately alert the team, enabling them to address the issue before it causes a bottleneck. This level of visibility ensures that production runs smoothly and efficiently, minimizing delays and maximizing output.
2. Improved Efficiency and Productivity
Efficiency is the lifeblood of manufacturing. Every minute of downtime or inefficiency can lead to lost revenue and missed deadlines. Production monitoring helps manufacturers identify inefficiencies, such as underutilized machines, slow production lines, or redundant processes.
By analyzing data on cycle times, downtime, and Overall Equipment Effectiveness (OEE), manufacturers can pinpoint areas for improvement and implement changes that boost productivity. For instance, if a particular machine is consistently underperforming, production monitoring can help determine whether it needs maintenance, recalibration, or replacement.
3. Enhanced Product Quality
Quality control is a top priority for manufacturers, as even minor defects can lead to customer dissatisfaction, returns, and damage to the brand’s reputation. Production monitoring systems track product quality at every stage of the manufacturing process, ensuring that defects are detected early and corrected before they reach the customer.
For example, if a machine starts producing parts that don’t meet quality standards, the system can flag the issue and halt production until the problem is resolved. This proactive approach to quality control not only improves customer satisfaction but also reduces the cost of rework and waste.
4. Predictive Maintenance to Reduce Downtime
Unplanned downtime is one of the biggest challenges in manufacturing. When a critical machine breaks down, it can bring the entire production line to a halt, resulting in significant financial losses. Traditional maintenance methods often rely on reactive approaches, where repairs are made only after a failure occurs.
For example, energy monitoring features can track the energy usage of machines and identify opportunities to reduce consumption. Similarly, by optimizing production schedules and reducing idle time, manufacturers can lower operational costs and improve profitability
5. Cost Savings and Waste Reduction
Manufacturing is a resource-intensive industry, and inefficiencies can lead to significant waste—whether it’s raw materials, energy, or time. Production monitoring helps manufacturers identify areas where resources are being wasted and implement strategies to reduce consumption.
For example, energy monitoring features can track the energy usage of machines and identify opportunities to reduce consumption. Similarly, by optimizing production schedules and reducing idle time, manufacturers can lower operational costs and improve profitability.
6. Improved Safety and Compliance
A safe working environment is essential for employee morale and productivity. Production monitoring systems can track safety metrics, such as equipment malfunctions and hazardous conditions, helping manufacturers implement preventive measures and reduce the risk of accidents.
Additionally, many industries are subject to strict regulatory requirements regarding product quality, safety, and environmental impact. Production monitoring ensures that manufacturers remain compliant with these regulations by providing accurate, real-time data on key metrics.
7. Data-Driven Decision-Making
In the past, manufacturing decisions were often based on intuition or historical data. While this approach may have worked in simpler times, today’s complex manufacturing environment requires a more data-driven approach.
Production monitoring systems provide manufacturers with actionable insights derived from real-time data. Whether it’s optimizing production schedules, allocating resources more effectively, or identifying trends in machine performance, these insights enable manufacturers to make smarter, faster decisions that drive growth and profitability.
8. Scalability for Growing Businesses
As businesses grow, their production monitoring needs become more complex. Traditional methods, such as manual data collection or outdated software, often struggle to keep up with the demands of a growing operation.
Modern production monitoring solutions, like M-Connect, are designed to scale with the business. Whether you’re a small manufacturer or a large enterprise, these systems can adapt to your needs, providing the flexibility and functionality required to support growth.
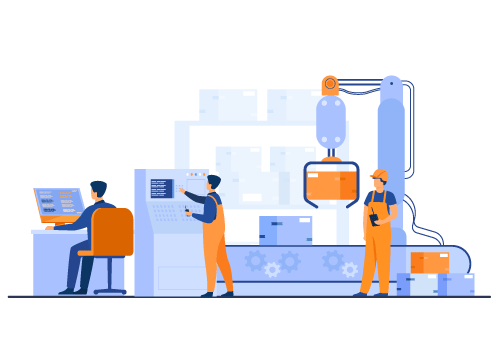
Boost Productivity with Mobile Access & Instant Alerts
Get Started TodayChallenges in Traditional Monitoring Methods
While the benefits of production monitoring are clear, many manufacturers still rely on outdated methods that limit their ability to compete in today’s market. Here are some of the key challenges associated with traditional monitoring methods:
Manual Data Collection
Traditional monitoring often involves manual data collection, where employees record production metrics on paper or spreadsheets. This approach is time-consuming, prone to errors, and lacks the accuracy needed for effective decision-making.
Lack of Real-Time Data
Without real-time data, manufacturers are forced to make decisions based on outdated information. This can lead to missed opportunities, delayed responses to issues, and inefficiencies in production.
Limited Visibility
Traditional methods provide limited visibility into production processes, making it difficult to identify bottlenecks and inefficiencies. For example, if a machine is underperforming, managers may not notice until it’s too late.
Inability to Predict Issues
Reactive maintenance is a common problem in traditional manufacturing. Without predictive analytics, manufacturers often wait for equipment to fail before taking action, resulting in costly downtime and repairs.
Scalability Issues
As businesses grow, their monitoring needs become more complex. Traditional methods are often unable to scale with the business, leading to inefficiencies and increased costs.
These challenges highlight the need for a more advanced, automated, and scalable solution—like M-Connect.
M-Connect: The Future of Real-Time Production Monitoring Software
M-Connect is a state-of-the-art production monitoring software designed to address the limitations of traditional methods. By leveraging the power of IoT (Internet of Things) technology, M-Connect provides real-time data on every aspect of the manufacturing process, from machine performance to employee productivity. Here’s how M-Connect is transforming production monitoring:
Seamless Integration with Existing Systems
M-Connect integrates seamlessly with existing machinery and software, making it easy for manufacturers to adopt the system without disrupting their operations.
Real-Time Data Collection and Visualization
With M-Connect, manufacturers can monitor production metrics in real time through an intuitive dashboard. This provides a clear, up-to-date view of operations, enabling quick and informed decision-making.
Predictive Analytics for Proactive Maintenance
M-Connect uses advanced analytics to predict potential equipment failures and bottlenecks. This allows manufacturers to schedule maintenance proactively, minimizing downtime and maximizing productivity.
Scalability for Growing Businesses
Whether you’re a small manufacturer or a large enterprise, M-Connect is designed to scale with your business. Its flexible architecture ensures that it can meet the needs of businesses of all sizes.
In short, M-Connect is more than just a monitoring tool—it’s a comprehensive solution that empowers manufacturers to optimize their operations and stay ahead of the competition.
Seamless Integrations for Smarter Manufacturing
Schedule Your Free TrialKey Features of Real-Time Production Monitoring Software
M-Connect offers a wide range of features designed to simplify production monitoring and drive operational efficiency. Here are some of the key features and benefits:
-
Machine Monitoring
Gain real-time updates on machine status to ensure smooth operations and minimize downtime.
-
Production Scheduling & Monitoring
Automate schedules, reduce idle time and ensure on-time deliveries with M-Connect’s advanced scheduling tools.
-
Proactive Machine Maintenance
Stay ahead of breakdowns with predictive alerts that notify you of potential issues before they occur.
-
Tool Life & OEE Monitoring
Monitor key metrics like tool life and Overall Equipment Effectiveness (OEE) to optimize performance and extend tool life.
-
Digital Check Sheets for Quality Control
Ensure compliance with intuitive, paperless workflows that streamline quality control processes.
-
Energy Monitoring
Track and manage energy consumption to lower costs and improve sustainability.
-
AI Dashboards & Reports
Use data-driven insights from AI-powered dashboards and reports to make smarter, faster decisions.
Conclusion
In today’s competitive manufacturing landscape, production monitoring is essential for achieving efficiency, quality, and cost savings. Traditional methods fall short, but M-Connect revolutionizes the process with real-time data, predictive analytics, and AI-driven insights. From machine monitoring and proactive maintenance to energy tracking and quality control, M-Connect empowers manufacturers to optimize operations, reduce downtime, and drive growth.
Embrace M-Connect to simplify manufacturing, boost productivity, and stay ahead of the competition. With this innovative solution, you can transform your production processes and unlock new levels of success.
FAQ - Frequently Asked Questions
Below, you can find the answers to the most common question of M - Connect.
M-Connect provides real-time data, predictive analytics, and automated reporting, helping manufacturers reduce downtime, increase productivity, and improve decision-making.
Yes, M-Connect seamlessly integrates with existing manufacturing systems, including IoT-enabled machines and legacy equipment.
M-Connect is ideal for various industries, including automotive, aerospace, textiles, electronics, and general manufacturing.
Real-time process monitoring continuously tracks manufacturing operations, allowing quick issue detection, reduced downtime, and improved efficiency.
A production monitoring system collects live data from machines and workers to track progress, detect inefficiencies, and maintain quality. It helps optimize production and reduce costs.
It means continuously tracking production and making quick adjustments. By using live data, manufacturers can prevent breakdowns, reduce waste, and ensure smooth operations.
Need support? Contact our team
Mon - Sat: 9 am to 6.30 pm
Leave a comment
Your email address will not be published. Required fields are marked *