Blogs
Start Your Live Demo Now!
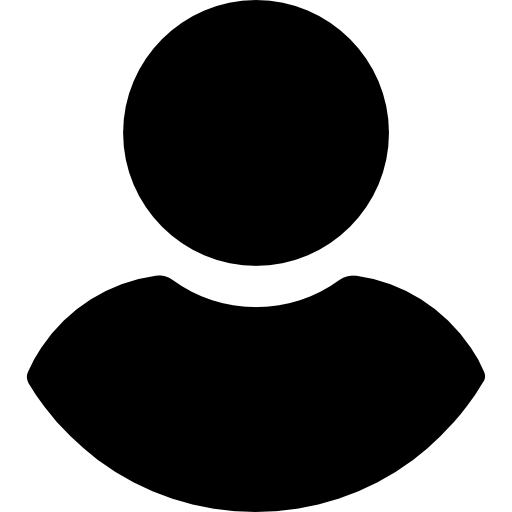
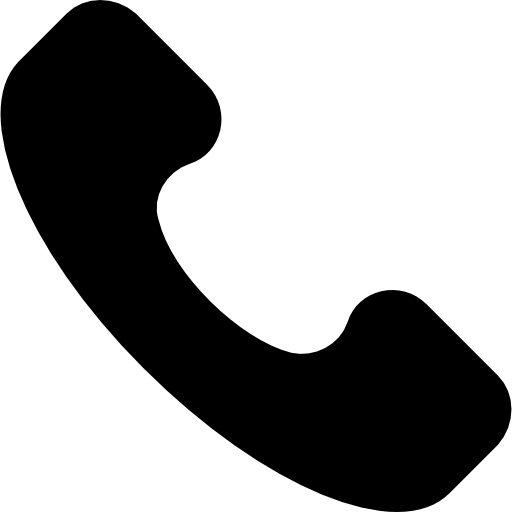
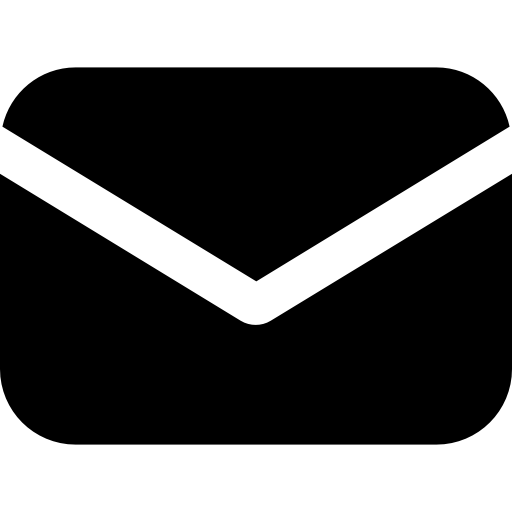
Best Practices for Implementing Work Order Management Systems
Introduction
Implementing an effective work order management system is crucial for organizations aiming to enhance operational efficiency, reduce downtime, and optimize resource allocation. Here, we'll explore the best practices for work order management, focusing on practical solutions and strategies to streamline your processes. Let's dive into the essentials of work order management and discover how you can elevate your operations to new heights.
Discover how implementing best practices can revolutionize your operations.
Table of Contents
Understanding Work Order Management
What is Work Order Management?
At its core, Work order management is the process of managing and tracking the lifecycle of work orders, from creation to completion. It ensures that maintenance tasks are efficiently executed, resources are optimally utilized, and any issues are promptly addressed.
Importance of Efficient Work Order Management
Efficient work order management is like having a fine-tuned system. It reduces downtime, minimizes errors, and boosts productivity. Adopting best practices can significantly improve organizations' operations.
- Improved Efficiency : Streamlines task management and reduces manual errors.
- Reduced Downtime : Ensures timely maintenance and quick response to issues.
- Enhanced Visibility : Provides real-time tracking and reporting.
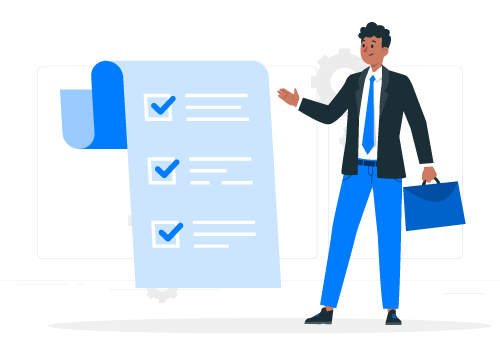
Enhance efficiency with mobile accessibility, real-time notifications, and seamless integrations.
Key Components of a Work Order Management System
Work Order Creation
Creating a detailed and clear work order is the first step toward effective management. It should include all necessary information, such as task description, location, required resources, and deadlines.
Work Order Assignment
Assigning the right task to the right person is crucial. This involves considering the skill set and availability of the personnel to ensure tasks are completed efficiently and effectively.
Work Order Tracking and Reporting
Monitoring the progress of work orders and generating reports helps identify obstacles and areas for improvement. It also ensures transparency and accountability in the process.
Best Practices for Work Order Management
Centralized System Implementation
Implementing a centralized system for managing work orders ensures that all information is accessible in one place. This reduces confusion and allows for better coordination.
Automation and Streamlining Processes
Automating repetitive tasks and streamlining processes can significantly reduce the time and effort required to manage work orders. This includes using digital tools and software to handle routine tasks automatically.
Preventive Maintenance Strategies
Preventive maintenance involves scheduling regular maintenance activities to prevent equipment failures. This proactive approach reduces unexpected breakdowns and extends the lifespan of equipment.
Effective Communication and Collaboration
Promoting open communication and team collaboration ensures everyone is on the same page. This includes regular updates, meetings, and the use of collaborative tools.
Adopt cutting-edge solutions like M-Connect to simplify work order management and boost productivity.
Leveraging Technology for Work Order Management
Digital Work Order Management Software
Selecting the right software is crucial. Using digital work order management software, like M-Connect, simplifies creating, assigning, and tracking work orders. Features such as real-time notifications and mobile access enhance efficiency.
Mobile Accessibility and Real-Time Notifications
Access to work order management systems via mobile devices makes information available anytime, anywhere. Real-time notifications keep everyone updated on task status.
Integration with Other Systems
Integrating work order management software with other systems, such as inventory management and CRM, ensures seamless data flow and better resource allocation.
Continuous Improvement in Work Order Management
Regular Monitoring and Evaluation
Continuously monitoring and evaluating the work order management process helps identify areas for improvement. Regular audits and reviews ensure that the system remains efficient and effective.
Training and Development
Providing regular training and development opportunities for employees ensures that they are well-versed in the latest tools and techniques for work order management.
Data-Driven Decision Making
Using data to drive decision-making helps identify trends, predict issues, and make informed choices that enhance efficiency.
Conclusion
Efficient work order management is the cornerstone of successful operations. Organizations can enhance productivity, reduce downtime, and optimize resource allocation by implementing best practices, leveraging technology, and fostering continuous improvement. Adopting a solution like M-Connect can further streamline processes, making work order management a breeze. Embrace these strategies to ensure your operations run well, driving success and growth. Ready to take your operations to the next level? Contact us today to learn more.
FAQ - Frequently Asked Questions
Below, you can find the answers to the most common question of M - Connect.
Work order planning outlines the tasks, resources, and timelines required to complete a work order. It ensures that all necessary information is available before the work begins.
Creating a work order in manufacturing involves:
- Detailing the task.
- Assigning it to the proper personnel.
- Specifying the resources required.
- Setting a deadline for completion.
Each stage requires careful management to ensure tasks are completed efficiently. The typical lifecycle includes:
- 1. Creation: Identifying the need and creating the work order.
- 2. Planning: Determining the resources and timeline required.
- 3. Assignment: Allocating the task to the appropriate team or individual.
- 4. Execution: Carrying out the task.
- 5. Review: Inspecting the completed work.
- 6. Closure: Closing the work order and documenting the outcome.
A work order typically includes a task description, location, assigned personnel, required resources, deadlines, and additional instructions or notes.
A workflow is a sequence of steps to complete a task, while a work order is a specific request for work to be done detailing what needs to be accomplished.
Essentials of a work order include task description, location, assigned personnel, required resources, estimated time for completion, and any additional instructions or notes.
Need support? Contact our team
Mon - Sat: 9 am to 6.30 pm
Leave a comment
Your email address will not be published. Required fields are marked *